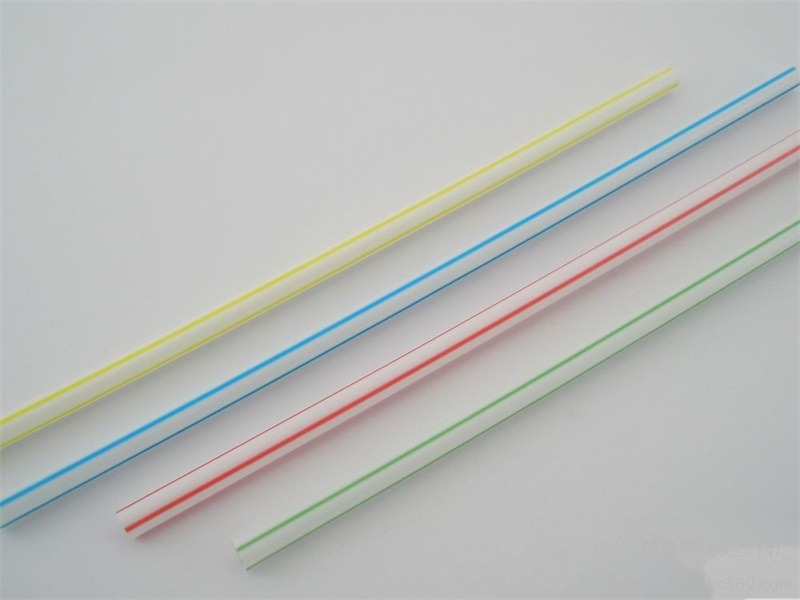
Экструдер для пластиковой соломки: от сырья до готовой продукции
Знаете ли вы, что скромная пластиковая соломинка проходит увлекательный путь от сырья до готового продукта, который вы используете ежедневно? В этой статье мы рассмотрим сложный процесс производства пластиковой соломинки , уделив особое внимание роли экструдеров для пластиковой соломинки.
Это всеобъемлющий обзор, который подчеркивает важность высококачественного оборудования для надежного и эффективного производства пластиковых трубочек . Понимая этот процесс, компании могут принимать обоснованные решения при инвестировании в индивидуальные линии по производству пластиковых экструдеров и вспомогательное оборудование.
Процесс экструзии
Стадия кормления
Путешествие начинается с этапа подачи, где пластиковое сырье , такое как гранулы или порошок, вталкивается в шнековый цилиндр экструдера. Подающий шнек играет здесь решающую роль, гарантируя, что сырье последовательно подается в экструзионный шнек, который затем вдавливает его в шнековый цилиндр.
Фаза плавления
Далее, экструзионный шнек перемешивает и сжимает пластиковое сырье, постепенно нагревая его до расплавленного состояния . Это достигается за счет комбинации механической работы шнека и внешнего нагрева, обеспечиваемого нагревательной муфтой. Высокая температура и давление в цилиндре шнека разрывают молекулярные цепи пластика, переводя его в расплавленное состояние.
Стадия экструзии
Наконец, расплавленный пластиковый материал поступает в головку экструдера через выпускное отверстие. Головка формирует расплавленный пластик в желаемый профиль . После экструзии непрерывный пластиковый профиль охлаждается и отверждается, образуя конечный продукт. Дополнительные устройства, такие как охлаждающие устройства, резаки и намотчики, могут быть присоединены к экструдеру для удовлетворения различных производственных потребностей.
Компоненты линии по производству пластиковых трубочек
Экструдер: Экструдер является сердцем линии по производству пластиковых трубочек. Он расплавляет термопластичный материал и формирует из него непрерывную трубку, которая затем охлаждается и разрезается на отдельные трубочки.
Охлаждающий блок: Охлаждающий блок быстро охлаждает экструдированный пластик, чтобы предотвратить деформацию и сохранить размерную точность. Это имеет решающее значение для обеспечения качества конечного продукта.
Режущий механизм: точные режущие механизмы разрезают непрерывную пластиковую трубку на отдельные соломинки одинаковой длины и с ровными краями.
Машина для сбора соломы: После резки машина для сбора соломы собирает солому, подготавливая ее к упаковке или дальнейшей обработке.
Основные характеристики машин для производства пластиковой соломки
Производственная мощность
Понимание производительности имеет решающее значение для эффективного планирования производства . Например, машина с 50-миллиметровым главным шнеком может производить до 30 кг/час, а с 65-миллиметровым главным шнеком — до 60 кг/час.
Совместимость материалов
В производстве соломинок используются различные виды пластика, такие как полипропилен (ПП). Обеспечение совместимости материалов имеет важное значение для оптимальной производительности и качества продукции .
Энергоэффективность
Энергоэффективные машины для производства соломы помогают снизить воздействие на окружающую среду и снизить эксплуатационные расходы . Например, машины, оснащенные инфракрасным нагревом, обеспечивают более быстрый нагрев, будучи энергоэффективными.
Характеристики двигателя и винта
Высококачественные машины оснащены надежными двигателями и специализированными шнеками . Например, трехфазный асинхронный двигатель мощностью 11 кВт обеспечивает больший крутящий момент и стабильность, а специализированный шнек для экструзии ПП обеспечивает большой объем экструзии и стабильную выгрузку.
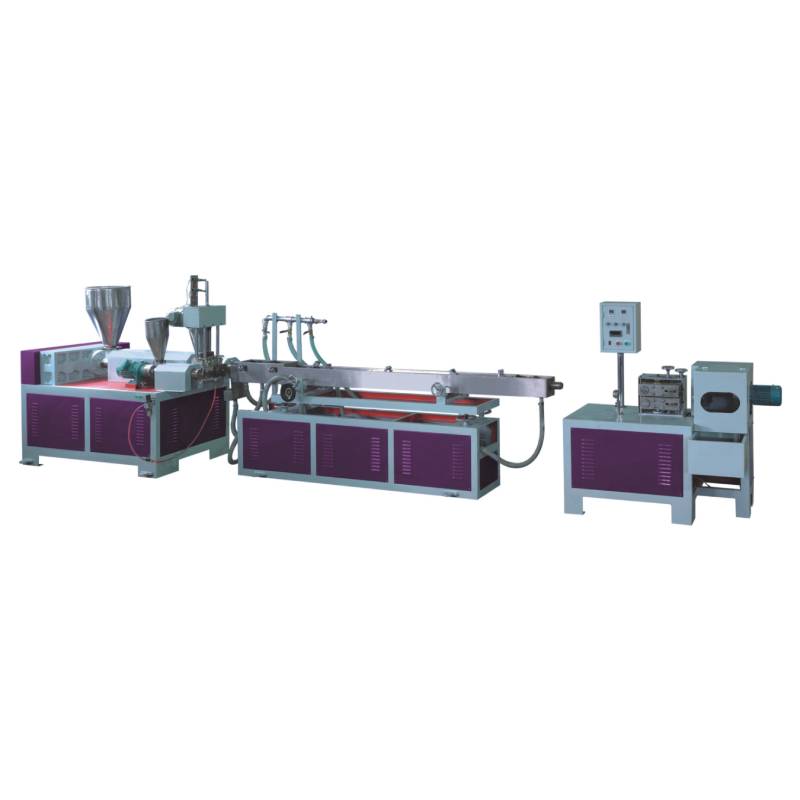
Преимущества применения экструдера для пластиковой соломы
Эффективность затрат
Пластиковая экструзия значительно дешевле альтернативных методов формования, таких как литье под давлением. Непрерывная работа пластиковых экструзионных машин снижает риск нехватки запасов и обеспечивает круглосуточное производство, что делает ее оптимальным выбором для крупномасштабного производства.
Гибкость и настройка
Пластиковые трубчатые экструдеры обеспечивают большую гибкость, позволяя производителям производить изделия с постоянным поперечным сечением, разными цветами и даже сложными формами. Этот метод хорошо подходит для создания изделий различных размеров, форм, цветов и профилей, соответствующих точным спецификациям дизайна.
Универсальность материала
Методы экструзии позволяют использовать широкий спектр термопластичных материалов , таких как ПВХ, полипропилен, полиэтилен и полистирол. Эта универсальность позволяет производителям выпускать продукцию с определенными свойствами, такими как гибкость, термостойкость, прочность и химическая стойкость.
Изменения после экструзии
Пластики остаются пластичными после выхода из экструдера, что позволяет проводить модификации после экструзии. Производители могут использовать такие инструменты, как ролики, башмаки и матрицы, чтобы корректировать форму пластика в соответствии со своими требованиями , повышая универсальность производственного процесса.
Экологические преимущества
Пластиковая экструзия может использовать переработанные материалы, сокращая отходы и способствуя устойчивому развитию . Кроме того, энергоэффективные машины помогают минимизировать воздействие производственного процесса на окружающую среду.
Повышение эффективности производства
Высокопроизводительные экструдеры могут производить до 100 кг/ч, обеспечивая эффективное и стабильное производство . Использование передовых технологий и надежных компонентов продлевает срок службы машин, обеспечивая долгосрочную надежность и снижение затрат на техническое обслуживание.
Заключение
Производство пластиковых трубочек — сложный, но увлекательный процесс, требующий высококачественного оборудования и точного контроля . Понимая процесс экструзии и ключевые компоненты линии по производству пластиковых трубочек, предприятия могут принимать обоснованные решения для повышения эффективности производства и качества продукции.
Инвестиции в современные экструдеры для производства пластиковых соломинок и вспомогательное оборудование могут привести к значительному повышению производительности и энергоэффективности, что в конечном итоге приведет к увеличению числа запросов и росту бизнеса . Для получения дополнительной информации о линиях по производству пластиковых экструдеров и вспомогательном оборудовании свяжитесь с нами!