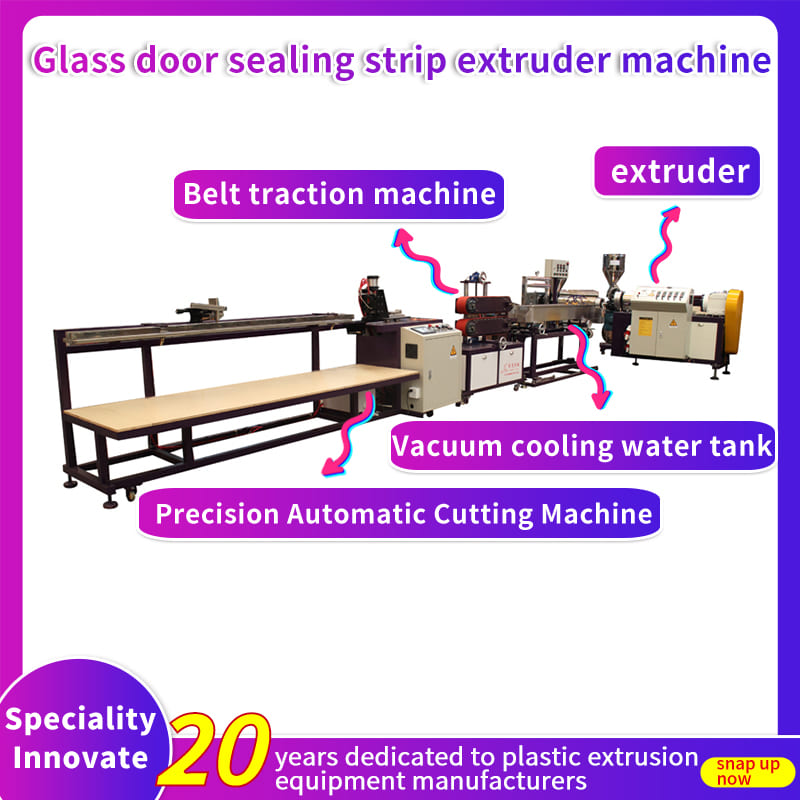
Как выбрать правильный экструдер для оконных и дверных уплотнителей?
Уплотнительные ленты для окон и дверей имеют решающее значение для энергоэффективности, защиты от непогоды и звукоизоляции в зданиях. Изготовление этих лент включает экструзию, процесс, который формирует такие материалы, как резина, ПВХ и ТПЭ, в непрерывные профили с использованием специализированного оборудования, называемого экструдерами. Выбор правильного экструдера имеет решающее значение для производства высококачественных уплотнительных лент, которые соответствуют определенным требованиям. В этой статье представлено полное руководство по выбору правильного экструдера для уплотнительных лент для окон и дверей с учетом различных факторов, таких как материал, типы экструдеров и требования к применению.
Понимание процесса экструзии
Процесс экструзии включает несколько основных этапов:
Выбор и подготовка материала: выбор подходящего материала (EPDM, силикон, ПВХ, TPE) на основе желаемых свойств, таких как устойчивость к атмосферным воздействиям, гибкость и экономическая эффективность. Затем выбранный материал подготавливается для подачи в экструдер.
Подача материала: Подача подготовленного материала в экструдер с помощью ленточного питателя для твердых материалов, таких как резина, или холодного питателя для более мягких смесей.
Нагрев и смешивание: Нагрев и смешивание материала внутри экструдера с помощью вращающегося шнека для обеспечения равномерного распределения температуры и давления, что делает его податливым для формования.
Формование профиля: продавливание нагретого материала через матрицу для создания желаемой формы и точного профиля поперечного сечения для уплотнителей окон и дверей.
Охлаждение и резка: Охлаждение экструдированного профиля в холодильной камере для его затвердевания с последующей резкой на отрезные станки необходимой длины.
Типы экструдеров
При производстве оконных и дверных уплотнителей используются несколько типов экструдеров, каждый из которых подходит для различных материалов и областей применения:
Одношнековые экструдеры: наиболее распространенный тип, подходит для большинства термопластичных материалов. Они просты и экономичны, но могут иметь ограничения по смешиванию материалов и теплопередаче.
Двухшнековые экструдеры: обеспечивают лучшее смешивание и теплопередачу, что делает их идеальными для более сложных материалов или процессов соэкструзии. Они более универсальны, но и более дороги.
Коэкструдеры: позволяют производить одновременную экструзию нескольких материалов, создавая многослойные уплотнительные полосы с различными свойствами в разных слоях, например, сердцевину из губчатой резины с более твердым внешним слоем.
Материалы, используемые для уплотнительных полос
Выбор материала зависит от желаемых свойств и области применения:
EPDM (этиленпропиленовый диеновый мономер): известен своей превосходной устойчивостью к погодным условиям и широко используется для наружного применения. Он обеспечивает хорошую устойчивость к ультрафиолетовому излучению и может выдерживать экстремальные температуры.
Характеристики: Исключительная стойкость к ультрафиолетовому излучению и озону, отличная эластичность и долговечность, выдерживает температуры от -40°C до 120°C.
Силиконовый каучук: обеспечивает превосходную гибкость и устойчивость к экстремальным температурам и часто используется в высокопроизводительных приложениях, где решающее значение имеет долговечность.
Характеристики: Термостойкость до 250°C, нетоксичен и безопасен для пищевых сред, очень гибкий.
ПВХ (поливинилхлорид): экономичный и простой в обработке, обычно используется для изготовления полос ПВХ, но может не обеспечивать такого же уровня устойчивости к атмосферным воздействиям, как резиновые материалы.
Характеристики: Легкий и экономичный, хорошие изоляционные свойства, умеренная устойчивость к атмосферным воздействиям.
TPE (термопластичный эластомер): сочетает в себе преимущества резины и пластика, обеспечивая гибкость и простоту обработки. TPE используется в приложениях, где необходим баланс между производительностью и стоимостью.
Нитриловые резиновые экструзии: Лучше всего подходят для стойкости к маслу и топливу и идеально подходят для гаражей, мастерских или мест, подверженных разливам масла. Они прочные, долговечные и идеально подходят для герметизации в тяжелых условиях.
Характеристики: Превосходная стойкость к жидкостям на нефтяной основе, отличная стойкость к истиранию, умеренный температурный диапазон (от -20°C до 100°C).
Неопреновые резиновые профили: подходят для герметизации как внутренних, так и наружных дверей и окон, обеспечивая баланс прочности и гибкости.
Характеристики: Хорошая стойкость к атмосферным воздействиям и химическим веществам, огнестойкие свойства, умеренная эластичность.
Факторы, которые следует учитывать при выборе экструдера
При выборе правильного экструдера необходимо учитывать несколько ключевых факторов:
Совместимость материалов: убедитесь, что экструдер совместим с выбранным материалом (резина, ПВХ, ТПЭ), чтобы обеспечить эффективную обработку и качественный результат.
Тип экструдера: Выберите подходящий тип экструдера (одношнековый, двухшнековый, соэкструдер) в зависимости от сложности материала и желаемых свойств уплотнительной полосы. Двухшнековые экструдеры идеально подходят для сложных материалов, требующих лучшего смешивания и теплопередачи. Соэкструдеры подходят для производства многослойных уплотнений.
Объем производства: Рассмотрите требуемый объем производства, чтобы определить производительность и скорость экструдера. Непрерывные процессы экструзии, предлагаемые машинами для производства пластиковых полос, позволяют производить большие объемы, снижая затраты на рабочую силу и повышая скорость производства.
Размеры и форма уплотнительной полосы: убедитесь, что экструдер может производить уплотнительные полосы с точными размерами и формами, необходимыми для конкретного применения. Линии экструзии уплотнительных полос из ПВХ предназначены для создания полос с точными размерами, гарантируя идеальное соответствие предполагаемым применениям.
Бюджет: Соотнесите стоимость экструдера с его производительностью и долговечностью. Более дешевые варианты могут сэкономить деньги на старте, но могут изнашиваться быстрее, в то время как более дорогие варианты часто служат дольше и обеспечивают лучшую производительность.
Гибкость: Определите, может ли экструдер обрабатывать различные приложения в различных отраслях промышленности. Машины для экструзии уплотнителей из ПВХ могут быть адаптированы для удовлетворения потребностей любого проекта, будь то производство магнитных уплотнителей для дверей, уплотнителей для окон или уплотнителей для душевых дверей.
Условия окружающей среды: Оцените условия окружающей среды, с которыми будут сталкиваться уплотнительные полосы. Для экстремальных погодных условий хорошим выбором будет EPDM, а силикон — лучший выбор для высокотемпературных сред.
Преимущества использования высококачественных уплотнительных полос
Использование высококачественных уплотнительных полос обеспечивает ряд преимуществ:
Энергоэффективность: уплотнительные полосы сокращают потери тепла зимой и приток тепла летом, повышая энергоэффективность и сокращая счета за электроэнергию.
Защита от атмосферных воздействий: они защищают от дождя, пыли и сквозняков, обеспечивая сохранность и безопасность внутренних помещений.
Долговечность: устойчив к износу, ультрафиолетовому излучению и перепадам температур, обеспечивает герметичность дверей и окон на долгие годы.
Снижение шума: уплотнители снижают уровень шума снаружи во время вождения, повышая комфорт.
Типы резиновых профилей для дверей и окон
Доступны различные типы резиновых экструдатов, каждый из которых имеет уникальные характеристики и области применения:
P-Seals: выглядят как буква P, с закругленной колбой и плоским стержнем. Колба сжимается, заполняя зазор и обеспечивая герметизацию, а стержень используется для крепления прокладки к подложке.
D-Seals: выглядят как буква D с полумесяцем, плоским снизу. Шарик обеспечивает герметизацию под давлением, например, когда дверь корпуса закрыта.
Уплотнения E-Seals: Это еще один распространенный тип экструдированных резиновых уплотнений.
Манжетные уплотнения: эти уплотнения имеют кромку, которая обеспечивает плотное прилегание к поверхности.
Процесс производства резиновых экструдатов
Процесс производства резиновых экструдатов включает несколько этапов:
Выберите и подготовьте резиновую смесь: Различные типы резины обладают разными свойствами, что делает их подходящими для разных сред и применений. Первый шаг — определить наиболее подходящий тип резины для продукта, который вы хотите изготовить. После того, как вы выбрали резину, вы можете смешать ее с добавками, чтобы добиться желаемых свойств.
Подача резины в экструдер: Затем резину следует подать в экструдер. Ленточный питатель обычно используется для твердых резин, в то время как холодный питатель используется для более мягких или более чувствительных смесей.
Экструзия: затем резину продавливают через матрицу для создания желаемой формы.
Формирование изделия: штамп специально разработан для изготовления точного профиля поперечного сечения, необходимого для уплотнителей окон и дверей.
Вулканизация: Затем резину вулканизируют, чтобы она затвердела.
Заключение
Выбор правильных экструдеров для уплотнителей окон и дверей требует тщательного рассмотрения совместимости материалов, типа экструдера, объема производства, бюджета и желаемых свойств уплотнителя. Понимая процесс экструзии, различные типы экструдеров и свойства различных материалов, производители могут выбрать наиболее подходящий экструдер для производства высококачественных уплотнителей, которые обеспечивают повышенную долговечность, улучшенную производительность и экономическую эффективность. Инвестиции в правильный экструдер гарантируют долгосрочные преимущества, включая энергоэффективность, защиту от атмосферных воздействий и снижение шума, что в конечном итоге способствует комфорту и устойчивости зданий.